Magnetic couplings
As a magnet specialist, BRUGGER has in-depth expertise and many years of experience in the development and manufacture of customised magnetic couplings. From conception to design to completion - the BRUGGER development team offers comprehensive support to find the optimum solution for your application.
Why are magnetic couplings advantageous in industry?
The term magnetic coupling is used as a generic term for a range of coupling types whose function is based on the effect of a magnetic field. Magnetic couplings are versatile tools that are used in numerous industrial applications thanks to their strong and safe power transmission. Magnetic couplings transmit torques or forces without direct contact. From the chemical and pharmaceutical industries to biotechnology, water management, compressors, measuring and dosing technology and hydraulics: magnetic couplings make a valuable contribution. The choice of the right magnetic coupling depends on the specific requirements of the application, such as torque, speed, temperature and ambient conditions.
Applications in industry
-
Pumps and fans: In these applications, magnetic couplings ensure reliable and low-maintenance torque transmission. They prevent leakage and protect the pump from overload.
-
Conveyor belts and material handling systems: Magnetic couplings enable conveyor belts to start and stop smoothly, which reduces damage to the transported goods. In the food industry, magnetic couplings can be used to permanently protect drives against overload.
-
The same applies in all areas where there is a risk of damage to the drive train or motor due to possible blockage. By using magnetic couplings, the frictional connection can be interrupted without damage, e.g. in packaging machines.
The advantages of this technology are obvious: contactless coupling enables use even under extreme conditions such as high temperatures, pressures, in a vacuum or in liquid and chemical environments. This opens up a wide range of unexpected possibilities.
There are various types of permanent magnet clutches, which differ in their design and mode of operation:
Face swivel clutch open

Face swivel clutch closed

Central rotary clutch


Eddy current clutch

Face rotary clutches:
Face rotary clutches utilise two opposing multi-pole magnet systems to generate the torque. This depends on the design, the magnet material used, the number of poles and the air gap. The smallest possible air gap maximises the torque. The partition wall should be made of a material that is both magnetically and electrically poorly conductive in order to avoid negative effects caused by eddy currents at high speeds. The high axial forces that can occur with face rotary clutches must also be taken into account. The starting speed must be selected so that skipping of the magnetic poles is prevented. The torque remains constant regardless of the speed.
Centre rotary clutches:
Centrally rotating clutches work with two interlocking magnet systems. The magnitude of the torque depends on various factors:
Mass: The more massive the magnets, the greater the torque.
Magnet material: The material properties of the magnet influence the strength of the magnetic force.
Number of poles: More poles lead to a stronger torque.
Air gap: The distance between the magnets should be minimised in order to achieve the maximum torque.
The separating wall between the magnets must be made of a non-magnetic material to prevent short circuits. It should also be electrically poorly conductive in order to minimise eddy current losses at high speeds. The starting speed must be carefully selected to prevent the magnetic poles from skipping. One advantage of central rotary clutches is that the torque remains constant over the entire speed range.
Eddy current magnetic clutches:
In eddy current clutches and brakes, a multi-pole magnetised magnet (usually the input) faces an aluminium or copper disc (usually the output). These clutches utilise the eddy current effect to enable power transmission. The permanent magnet generates a magnetic field that induces eddy currents in a conductive material. The interaction of these magnetic fields generates a force that enables the coupling.
The torque or braking torque generated depends on the size of the design, the magnet material used, the number of poles, the air gap and the relative speed. The transmitted torque or braking torque increases with increasing speed. This is why this system is also known as an eddy current brake. The special feature of such an induction brake is its wear-resistant function, as it works with eddy currents generated by magnetic fields without mechanical friction. If necessary, the torque can be easily regulated by axial displacement, i.e. by adjusting the air gap and thus the effective flux. Due to the eddy currents generated, these clutches and brakes heat up considerably with increasing speed, which significantly reduces the achievable torque or braking torque depending on the temperature reached.
Hysteresis magnetic clutches:
These clutches use a ferromagnetic core that is magnetised by an external magnetic field. The magnetisation of the core enables a permanent coupling.
Linear magnetic brakes are a special type of hysteresis magnetic clutch that are used for the controlled deceleration or stopping of moving parts, e.g. for thread, rope or belt tension. Linear magnetic brakes function reliably, even in the event of power failures, and are ideal for reducing speed in production lines, e.g. on conveyor belts
Focus on your wishes - our expertise for your project
As a full-service provider for your production, we offer maximum flexibility:
- Independent of material: Whether metal housings, plastic parts or other materials - we manufacture according to your requirements.
- Independent of quantity: From small batches to large-scale production - we adapt to your required quantity.
- Production-independent: Thanks to our comprehensive expertise and state-of-the-art machinery, we can realise a wide range of manufacturing processes.
Magnetic components are just one example of our expertise. We would be happy to advise you on the development of customised solutions that are perfectly tailored to your requirements.


What is a magnetic coupling and how does it work?
A magnetic coupling is a non-contact torque transmission device based on magnetic fields. Unlike conventional mechanical couplings, which rely on direct contact and friction, magnetic couplings utilise the attractive and repulsive forces of magnets to create a connection between two shafts. A magnetic coupling typically consists of two main magnetic components arranged in such a way that they interact. When the input part rotates, it generates a magnetic field that acts on the output part and sets it in motion. Torque is transmitted without contact by the magnetic flux between the two parts.
Magnetic couplings with axial force transmission can transmit torques, but here additional axial forces are always generated, which must be absorbed by appropriate bearings.
Magnetic couplings with radial force transmission utilise the radial force between two magnets to create the connection. The forces here act centred to the axis and are usually easier to support, as the shafts already have to be supported anyway and the axial forces are usually low.
Advantages of magnetic couplings
-
Wear-free: As there are no direct mechanical contacts, magnetic couplings are not subject to wear. This leads to a longer service life and lower maintenance costs.
-
High reliability: Magnetic couplings are less susceptible to failure due to vibrations, shocks or dirt. The non-contact transmission reduces the risk of mechanical damage.
-
Smooth starting and braking processes: Magnetic couplings allow machines to start and stop smoothly, as the torque transmission is dampened by the magnetic field. This protects the drive elements and reduces wear.
-
Separation of drive and output: Magnetic couplings make it easy to separate the drive and output sides. This is particularly useful in emergency situations or during maintenance work.
-
High efficiency: Magnetic couplings can achieve a high level of efficiency as no energy is lost through friction.
-
Suitable for demanding environments: Magnetic couplings can be used in environments with high temperatures, moisture or aggressive chemicals as they do not require sensitive seals or lubricants.
Do you have any questions or would you like specific technical advice on possible customised magnetic systems for your application? Please contact us:
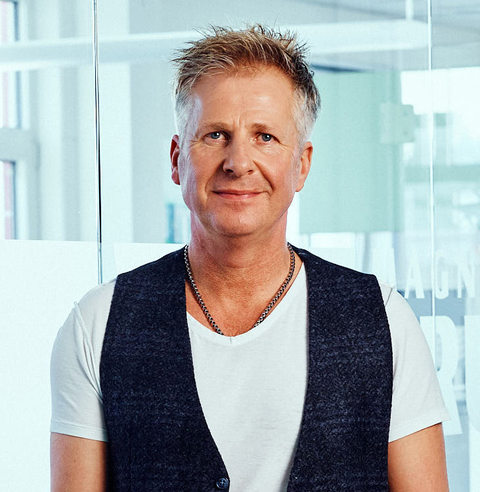
Stephan Zenner
Sales Consultant - Technical Application Consultant
Responsibility: Germany postcode 6/7/8/9/0, as well as Croatia, Austria, Switzerland, Slovakia, Slovenia, Czech Republic and Hungary.
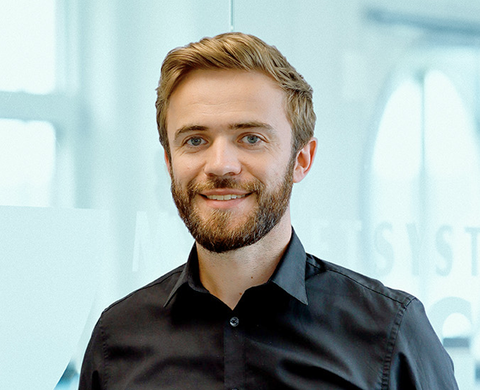
Quentin Burdel
Sales Consultant - Technical Application Consultant
Responsibility: Europe with focus on France, as well as America, Asia Africa and Oceania