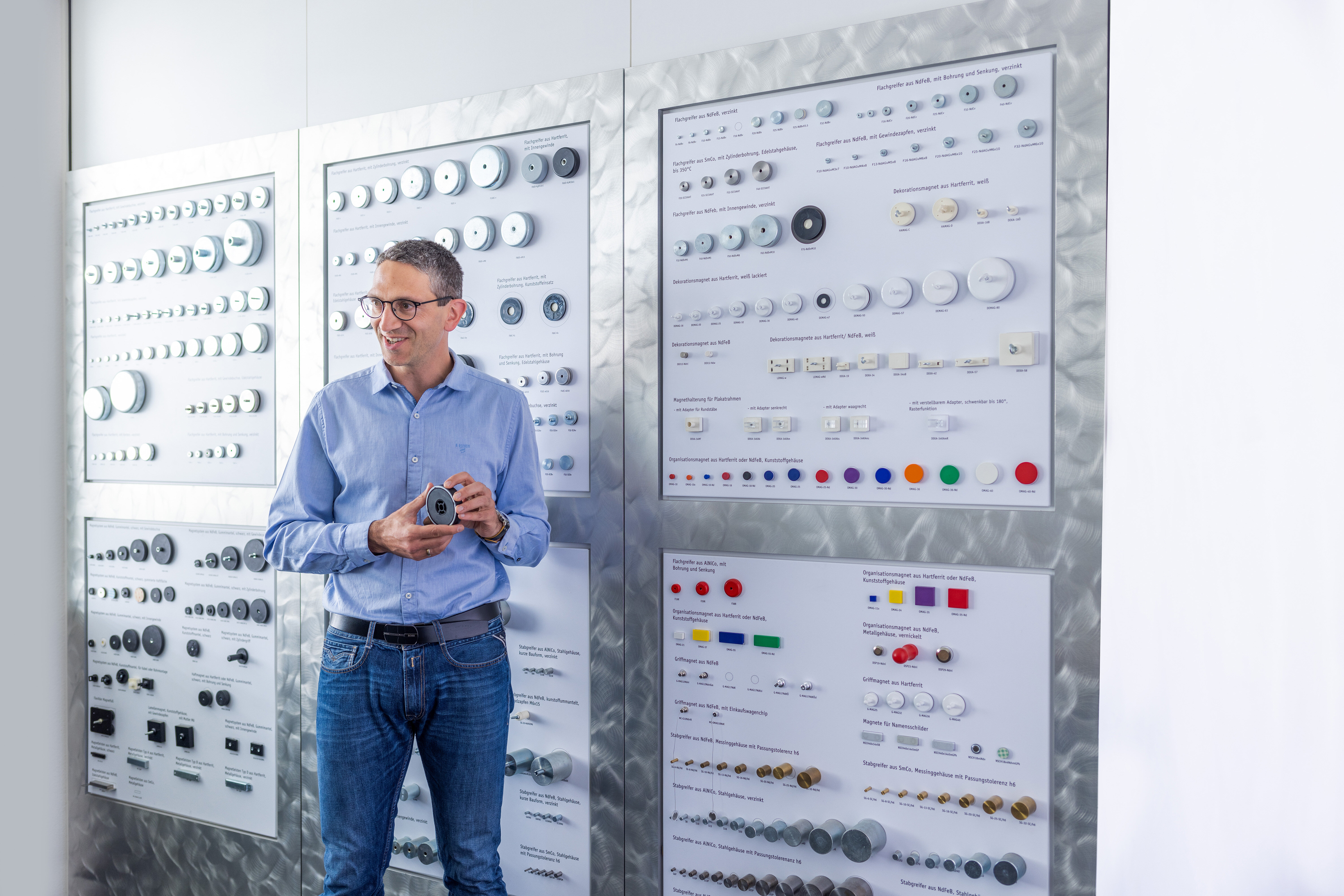
BRUGGERpedia
From development to production
We are happy to take on technical challenges and offer expert advice and customised magnet systems for almost any application. With our own toolmaking department and extensive machinery, we can also produce prototypes at short notice. Our plastic and metal processing machines, such as plastic injection moulding machines, automatic punching and turning machines and eccentric presses, enable us to manufacture many individual parts directly in-house. We source additional production parts mainly from suppliers in the region (local sourcing). We have been certified to DIN EN ISO 9001 since 1999 and regularly review our processes and procedures to ensure that we can always offer our customers guaranteed quality with an excellent price-performance ratio. We also always check whether existing components or tools can be utilised.
You too can benefit from our more than 60 years of experience and expertise, which we are happy to share with you.
Worth knowing
Temperature and adhesive force
Please note the respective temperature specifications for the maximum operating temperature of our magnetic systems. In general, the adhesive force of the systems is reduced with increasing temperature for every magnetic alloy. The maximum operating temperature specified in the catalogue indicates the temperature up to which the systems can be used without being damaged. If this limit is exceeded, this has an effect on plastics, adhesives and/or the magnetic force.
The following diagrams illustrate the dependence of the adhesive force on temperature and other influencing factors such as air gap and counter anchor:
Schematic representation of the dependence of adhesive force and temperature

Schematic representation of the dependence of adhesive force and air gap

Schematic representation of the dependence of the adhesive force on the counter-anchor material

General safety data sheet
The safety data sheet describes products with regard to safety requirements. The information is not intended as a guarantee of properties.
Surface protection
The steel parts are galvanised as standard and then passivated in blue. The magnets are bright nickel-plated.
Magnetisation
All magnet systems supplied by us are always manufactured with the same magnetisation, i.e. the arrangement of the poles on the holding surface is always the same for each alloy.
HF/AlNiCo

HF/AlNiCo

NdFeB/SmCo

NdFeB/SmCo

It is essential that you observe the following when handling magnets:
In order to produce strong magnets or for complex multipole magnetisation, a strong, short current pulse is passed through a specially developed coil. This is called pulse magnetisation. This method can be used to generate very high magnetic fields, which are required to saturate (fully magnetise) certain materials.
The respective type of magnetisation depends on the desired application, the design and the material of the magnets used. For example, different types of magnetisation can be used to achieve different magnetic fields and holding forces with otherwise identical designs. The raw magnet used also plays a role. If it is an anisotropic magnet, the first four types of magnetisation mentioned here are generally used. In the case of an isotropic magnet, the latter two types of magnetisation are generally used.
Axial

Axially magnetised, anisotropic
Axial magnetisation describes how magnets are aligned during production where the poles are at opposite ends of the magnet (e.g. discs, cylinders). This orientation follows the length of the magnet, hence the term "axial".
Axial sector-shaped

Axial sector-shaped magnetisation, anisotropic
Sector-shaped magnetisation means that a material is not evenly magnetised, but has different magnetisation forces or directions in different areas.
Two-pole

Two-pole magnetised, anisotropic
With two-sided multipole magnetisation, both sides of the material are magnetised. To ensure that the poles do not get in each other's way or that the material is not partially demagnetised again, the poles on both sides must be offset by one pole. This means that the north pole meets the south pole again.
Diametral

Diametrically magnetised, anisotropic
Diametral magnetisation is a magnetisation direction in which the magnetic poles lie on opposite surfaces of a magnet that runs through the diameter of the magnet. This orientation is particularly common in disc and bar magnets as well as ring magnets.
Multipole

Multi-pole surface magnetisation, isotropic
Multipole magnetisation means that a magnet or material has more than two poles (north and south). These poles are arranged in a specific pattern, usually alternating, and create a more complex magnetic field than a dipole magnet.
Radial

Radial magnetisation, isotropic
With radial magnetisation, the magnetic field runs from the centre to the outer edge of the magnet. This alignment is used in sensors and magnetic assemblies and offers precise magnetic control.
Anisotropic
Unequal in structure in relation to the spatial directions. For magnets, this means that a strong magnetic field is applied during production and thus a device of "elementary magnets" is achieved. During subsequent magnetisation with the field direction in the fixture axis, better results are obtained for the magnetic values than in other spatial directions.
Isotropic
The same structure in relation to the spatial directions. For magnets, this means that none of the spatial directions is preferred when magnetising in the direction of a specific axis.
Preferred direction
Orientation of the magnetic crystals in a specific direction.
Permanent magnet
A permanent magnet is a magnet that displays and retains a static magnetic field.
Operating temperature
The operating temperature indicates the temperature up to which magnets can be used. In general, the adhesive force of magnetic systems is reduced at higher temperatures. Strong heating (temperature rises above the so-called Curie temperature) leads to irreversible demagnetisation.
Air gap
Space or distance between two opposing surfaces of a magnet or magnet system and in turn a magnet or magnet system or a magnetisable object. The space between the surfaces must consist of non-magnetisable material.
Magnetism
Magnetism is a physical phenomenon, a sub-area of electromagnetism as one of the four fundamental forces of physics. Magnetism is described with the help of the magnetic field H and the magnetic flux density B. Magnetism is caused by moving electrical charges or by magnetic (orbital) torques and intrinsic torques (spin) of electrons. Magnetism manifests itself in a force mediated by the magnetic field, emanating from magnetic objects (such as permanent magnets) or acting on them (such as iron).
Magnetisation
The elementary magnetic particles are aligned by a magnetic field. This makes the object magnetic.
Magnetic system
Combination of a magnet with other components made of metal and/or plastic.
Rare earths (SE)
are among the metals, or the 14 chemical elements in the periodic table that follow lanthanum, the lanthanides, as well as scandium and yttrium. Neodymium belongs to the light rare earths (cerium group).

The demagnetisation curves shown here are depicted in the second quadrant of the hysteresis of permanent magnetic materials. These show the differences between neodymium-iron-boron, samarium-cobalt, aluminium-nickel-cobalt and hard ferrite magnets, which we use in our magnet systems.
The remanence B is the measure of the magnetic induction that remains in the magnet after magnetisation.
The coercive field strength Hc describes the magnetic field strength required to make the magnetic induction in the magnet disappear. This happens when a permanent magnet is placed in an inversely polarised magnetic field with a coercive field strength Hc.

Neodymium-iron-boron (NdFeB)
Alloy of neodymium, iron and boron with the composition Nd2Fe14B.
NdFeB magnets have a hardness of 560-580 HV and are less brittle than alloys of HF and SmCo. The material can be machined with diamond tools and wire and die-sinking EDM. Due to the strong oxidation in the raw state, they are mainly offered nickel-plated or galvanised. NdFeB magnets have a very high energy density, so that very high holding forces can be achieved at maximum saturation. Depending on the composition of the alloy, they can be used in temperature ranges from - 40°C to + 200°C*.
Samarium-Cobalt (SmCo)
Alloy of the rare earth metal samarium (Sm) with the metal cobalt (Co).
Alloy structures:
SmCo5 (without iron content)
Sm2Co17 (with 20-25 % iron content)
These magnets have a hardness of 500-700 HV and are therefore brittle. They can be machined with diamond tools and wire and die-sinking EDM. Due to their high cobalt content, they are more expensive than other magnet materials. SmCo magnets oxidise only slightly and have good chemical resistance. Due to their high energy density (approx. 30-40% less than NdFeB magnets), high holding forces can be achieved at maximum saturation. They can be used in temperature ranges from -40°C to +350°C*. Minor cracks in the magnetic material have no effect on the holding force.
Aluminium-nickel-cobalt(AlNiCo)
Alloys of aluminium, iron, nickel, copper and cobalt. Permanent magnets are made from these alloys using casting or sintering techniques.
These magnets have a hardness of 510 HV and can be processed using diamond tools (grinding, drilling), wire and die-sinking EDM, water jet cutting, hard turning and hard milling. Due to their magnetic properties, magnets made of AlNiCo must have a large length in the direction of magnetisation in order to have good demagnetisation resistance as open magnets. AlNiCo magnets are very temperature-resistant and can be used in temperatures ranging from -270°C to + 450°C*.
Hard magnetic ferrites (HF)
Are made from iron oxide and strontium carbonate.
Strontium ferrites Composition: SrFe12O19
These magnets have a hardness of 480-580 HV and can be machined using diamond tools and water jet cutting. In contrast to rare earth magnets, ferrites have a significantly lower magnetic energy density. These raw materials are available in large quantities and are therefore very inexpensive.
Chipping on sharp edges of the ferrites is permitted insofar as the original shape of the magnet and thus its function are still given. If 100% flawless edges are required, this must be explicitly stated. Minor cracks in the magnet material have no influence on the adhesive force.
Magnets made of HF can be isotropic (no preferred direction of the elementary particles -> lower adhesive force) or anisotropic (elementary particles are preferentially orientated -> higher adhesive force). HF magnets can be used in temperature ranges from -40°C to + 250°C*.
The material is hard and brittle and can only be machined with diamond tools. HF is also resistant to oxidation and weathering and has good chemical resistance.
* However, the maximum operating temperature varies and depends crucially on the actual alloy, the area of application, the associated materials and the geometry of the magnet. For precise information on the temperature range of your magnet system, please refer to our product catalogue or contact us personally.
Before the discovery of the connection between magnetism and electricity, magnetic phenomena could only be observed and utilised using natural magnetic iron stones. One important application of this was the compass, the principle of which was already known in pre-Christian China and in ancient Greece. The magnetic iron stones were named after the landscape of Magnesia in Greece, where they were found early on. The removal of iron spikes from the body using magnetic forces was also practised and described in ancient Indian medicine.
In the 13th century, the first records were made in Europe about the magnetisation of compass needles and other important findings about magnetism, such as knowledge of the magnetic properties of the earth's sphere.
Through systematic experiments, the first "artificial" magnets were created in the following period. For example, the lines of force were concentrated at the poles of magnetic stones with small iron caps, or magnetic steel needles were bundled together. Even in the 18th century, magnetism was still unexplained, but nevertheless fascinating. The discovery and utilisation of the magnetic properties of rare earth combinations such as NdFeB, SmCo, AlniCo have led to enormous increases in performance in recent years.

Some of our magnet systems are a combination of a permanent magnet core together with an iron housing. We can achieve increased holding forces by using various options for joining.
You can see which options are available in the following illustration. The holding force of the magnetic core serves as a reference for the following options:
Magnetic core

Factor 1
Magnetic core with iron return

approx. factor 1.3
Magnetic core with iron return and centre pole

approx. factor 4.5
Magnetic core in U-shape iron

Factor 5.5
Magnetic core in round iron housing (flat pot magnet)

approx. factor 6
Ring magnet in iron housing with
centre pole

approx. factor 7
Magnetic bar made of AlNiCo in round iron housing (pot system)

Factor 7.5
Magnetic core with pole shoes

approx. factor 16
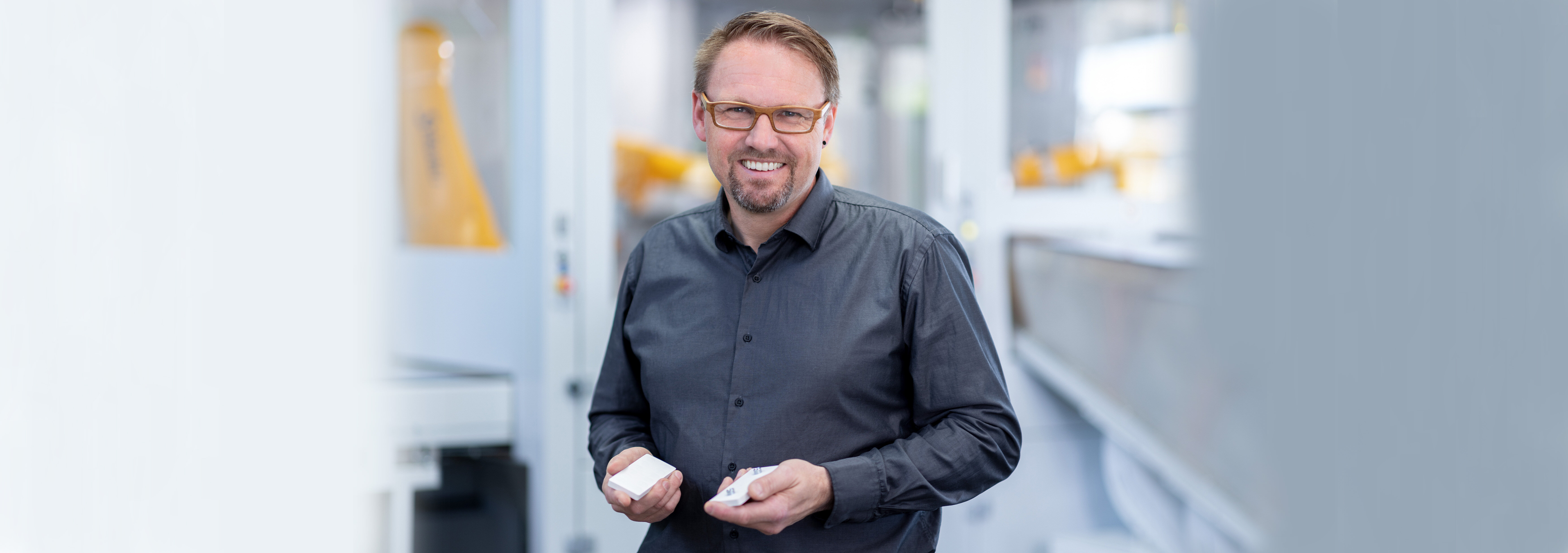
"We are ready to take on any technical challenge - from development to production."