Magnetic rotors and stators
Magnetic rotors are versatile and play an important role in modern electrical engineering, both in the generation and utilisation of electrical energy. We at BRUGGER look forward to working with you on the development and production of your magnetic application! Feel free to contact our experts for a non-binding consultation.
Why are permanent magnet rotors essential for modern electric motors and generators?
Rotors with permanent magnets are essential components of many modern electric motors and generators. The operation of these rotors is based on the generation of a constant magnetic field by the permanent magnets strategically placed around the rotor.
Permanent magnet rotors are widely used in various applications, including electric vehicles, industrial drives, compressors, wind turbines and household appliances. The choice of magnetic materials, such as neodymium-iron-boron, plays a crucial role in the performance and cost of these machines.
Magnetic rotors have decisive advantages: They increase the efficiency and power density of motors, as they do not require any additional energy to generate the rotor field. This advantage makes them highly versatile - from tiny, high-precision drives in electronic devices to powerful motors in industrial applications and transport.
Application example for magnetic rotors and stators
Development of a magnetic rotor


Areas of application
Magnetic rotors and stators are used in:
- Electric motors: In electric motors, magnetic rotors convert electrical energy into mechanical energy. They drive a wide range of devices, from household appliances to vehicles and industrial machines.
- Generators: In generators, magnetic rotors convert mechanical energy into electrical energy. They are used in power stations, wind turbines and other power generation plants.
Advantages:
- Efficiency: Magnetic rotors can be very efficient as they generate little friction and can reach high speeds.
- Reliability: Magnetic rotors are very reliable and durable as they contain few wearing parts.
- Versatility: Magnetic rotors can be manufactured in a variety of sizes and shapes and are therefore suitable for many different applications.
Focus on your wishes - our expertise for your project
BRUGGER offers you maximum flexibility:
Everything from a single source: from the idea to the finished product - all production steps are carried out in-house.
Choice of materials: Whether metal housing, plastic housing or other materials - we adapt to your requirements.
Customised quantities: Whether small series or large runs, we produce exactly the quantity you need.
Manufacturing diversity: Thanks to our extensive expertise and modern machinery, we can utilise a wide range of manufacturing processes.
More than just magnets: We are your competent partner for all types of products - contact us!


What are magnetic rotors and stators and how do they work?
Magnetic rotors essentially consist of two main components: a rotor (the rotating part) and a stator (the stationary part). Both parts can contain magnets, either permanent magnets or electromagnets. The magnets in the rotor and stator are arranged in such a way that they either attract or repel each other. These forces generate a torque that sets the rotor in motion.
Magnetic rotors made of permanent magnets utilise the property of these magnets to generate a permanent magnetic field without the need for an external power supply. Due to the contactless power transmission, the efficiency is high and since no moving parts are involved, magnetic rotors made of permanent magnets are very low-maintenance.
Electromagnetic rotors use a changing magnetic field to induce electrical currents in coils, which in turn generate magnetic fields. These fields interact with the magnets in the rotor to create the rotary motion used in a variety of devices and machines. In many cases, the movement of the rotor is generated by electromagnetic induction.
- Induction: The rotary movement of the rotor induces an electric current in the stator.
- Torque: The interplay between the magnetic fields of the rotor and stator generates a torque that keeps the rotor in motion.
-
Magnetic material: The rotor is typically made of a ferromagnetic material with high coercivity, such as neodymium-iron-boron (NdFeB), samarium-cobalt (SmCo) or ferrite. These materials retain their magnetisation even after the magnetising field has been removed.
-
Magnetisation: During production, the permanent magnets on the rotor are magnetised in a specific arrangement and polarity. This creates a specific magnetic field pattern.
Do you have any questions or would you like specific technical advice on possible customised magnetic systems for your application? Please contact us:
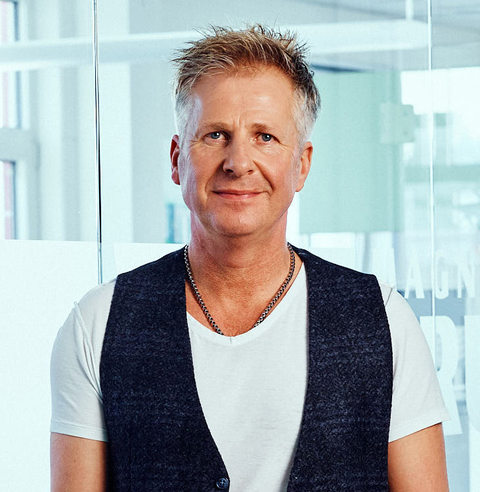
Stephan Zenner
Sales Consultant - Technical Application Consultant
Responsibility: Germany postcode 6/7/8/9/0, as well as Croatia, Austria, Switzerland, Slovakia, Slovenia, Czech Republic and Hungary.
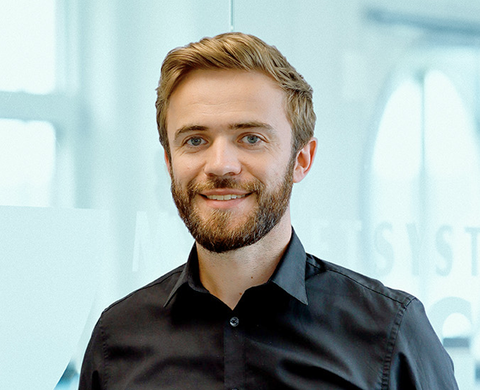
Quentin Burdel
Sales Consultant - Technical Application Consultant
Responsibility: Europe with focus on France, as well as America, Asia Africa and Oceania